MOPPET Valve
Outstanding Reliability
MOPPET® valves provide outstanding reliability, in even the most demanding service. The revolutionary design incorporates key features of field-proven Manley® radiused disc elements with additional innovations in valve technology. The design is custom-engineered for each application resulting in a valve that delivers consistently longer run times and reduces total life cycle costs.
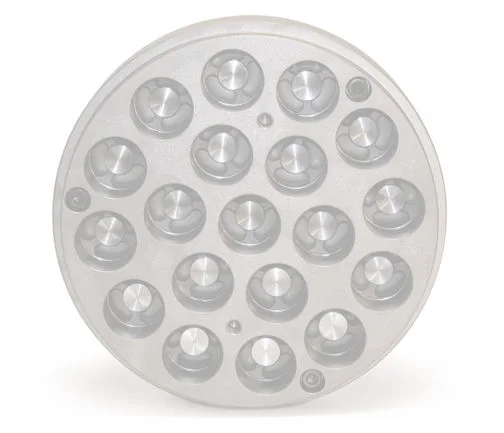
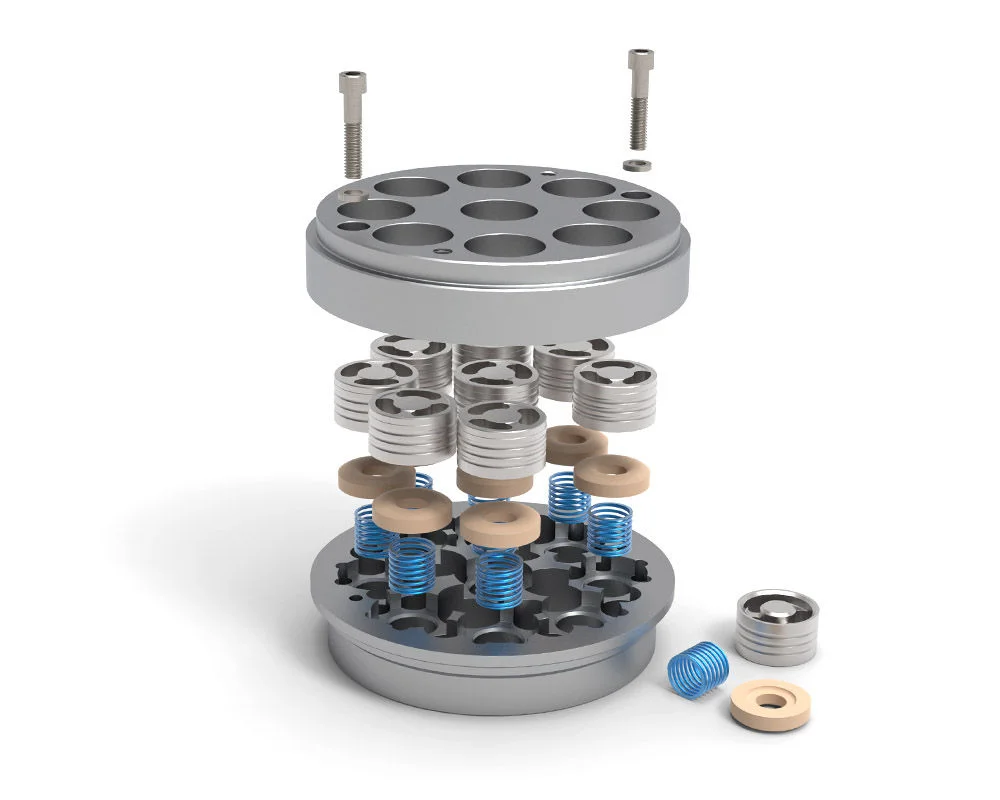
Robust Sealing Elements
A MOPPET valve consists of a series of small, identical, radiused-disc elements that operate independently of each other to effectively disperse liquids and debris. Each element is made of durable, lightweight thermoplastic material, designed to provide outstanding resistance to damage and wear from entrained material. The low-mass thermoplastic disc reduces impact velocities while the standard radiused sealing surface deflects debris.
Radiused elements are thick (0.35 inch/8.89 mm) and have a centerline diameter of only one inch (25.4 mm), making them extremely stiff and resilient. They exhibit low bending stresses and withstand high impact forces caused by extreme pressure, gas mole weight, driver speed, or the presence of incompressible matter in the gas.
Advanced Spring Design
Springs and spring pockets in MOPPET valves are designed for extended performance in dirty service.
- Spring pockets have generous vent holes that eliminate build-up of incompressible materials that can damage springs
- High lifts and more space between the spring coils allow debris to pass freely through the valve
- Springs have significantly taller free length, allowing for large wire diameter that reduces torsional stress and makes the springs more resistant to damage from debris
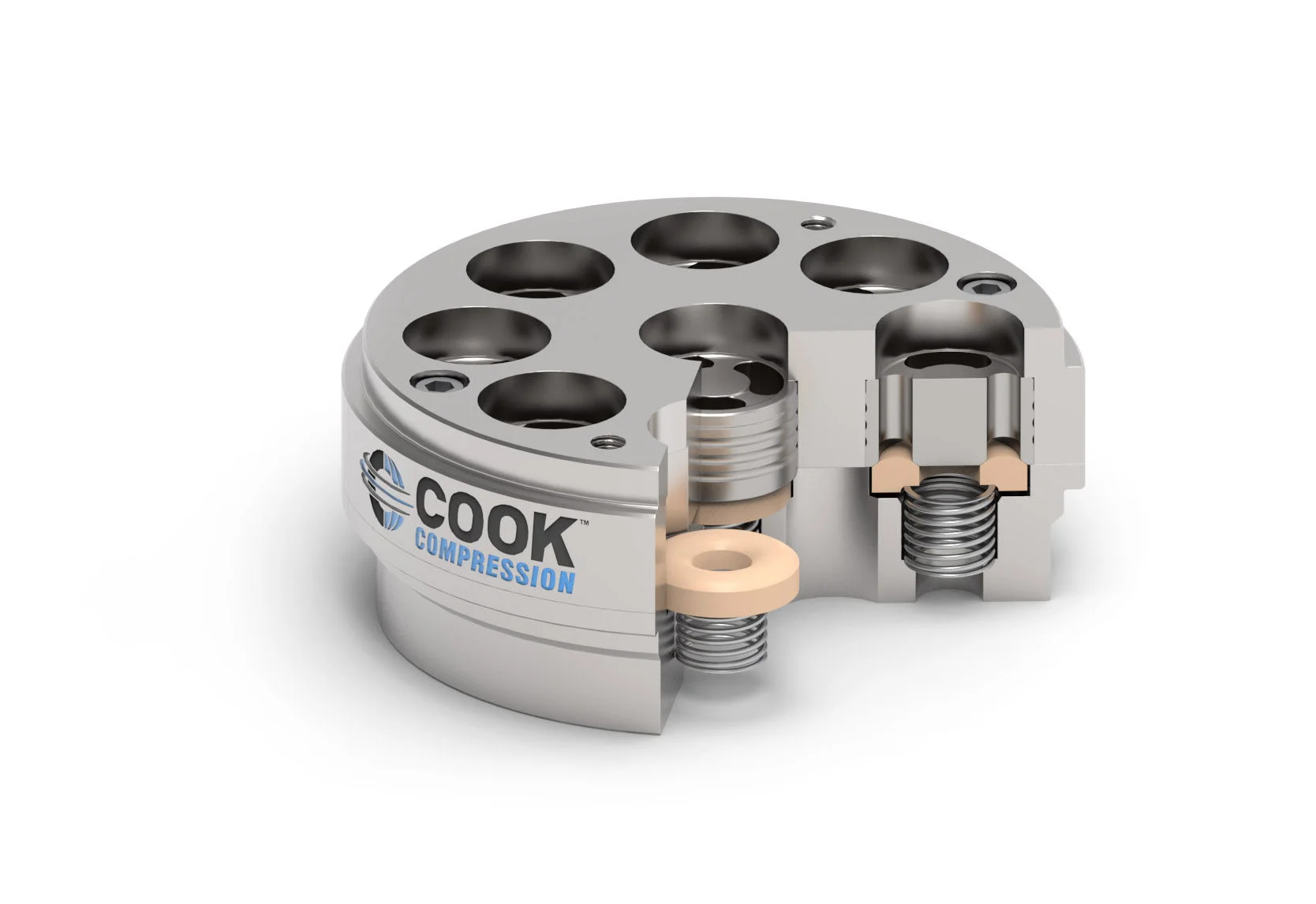
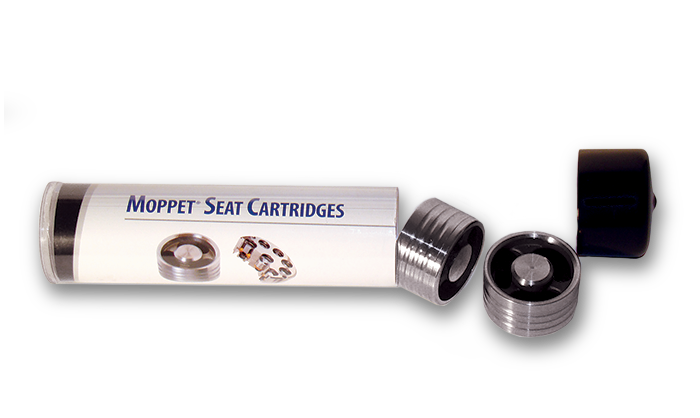
Commonality of Parts
MOPPET cartridges are identical and universally interchangeable – from valve to valve and compressor to compressor. This commonality of parts significantly reduces inventory costs. Any compressor you have will use the same radiused-disc element and seat cartridge, plus one of a small number of color-coded springs. Repair technicians remain fully prepared with only a minimal number of spare parts on hand. All items are stocked and readily available from Cook Compression.
Field Repairability
The legacy MOPPET valve design makes field repairs simple and economical. Sealing elements and springs are combined with a seat in a convenient cartridge that can be removed and replaced in minutes with a hydraulic press. Repairs can be performed in the field, with no lapping, grinding or machining required.
Elements and springs are replaced each time a valve is serviced, but cartridges are replaced only when damaged or worn. Incremental replacement reduces costs and helps maximize the utility of each component. MOPPET cartridges are precision-manufactured from 17-4 stainless steel for exceptional corrosion resistance on critical seating surfaces.
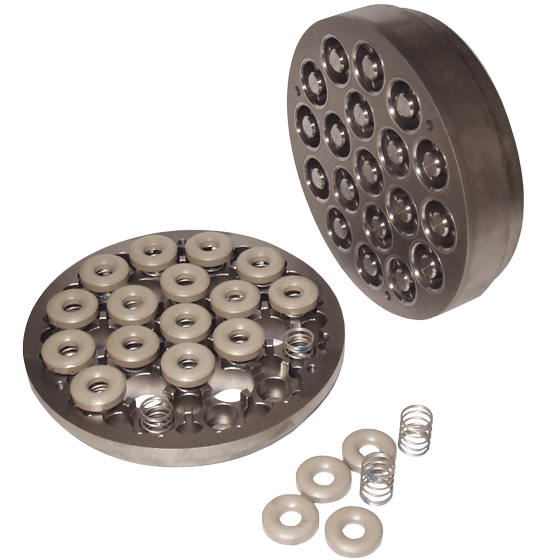
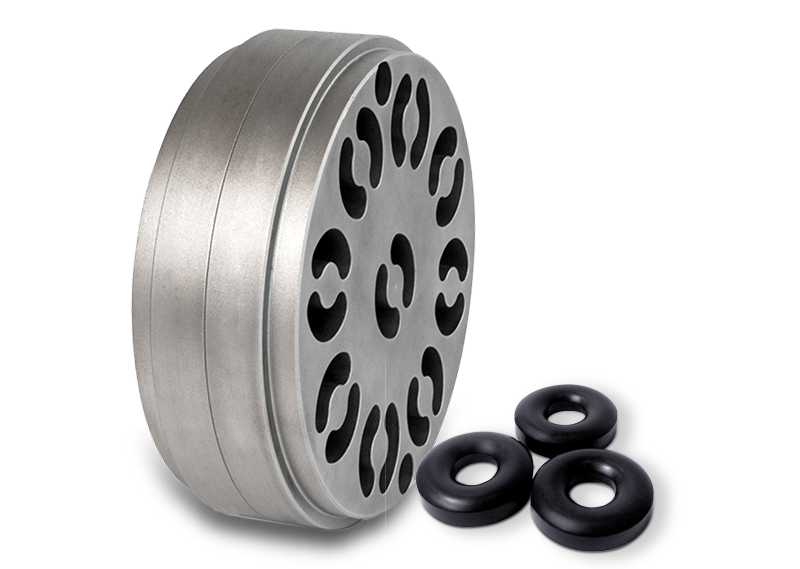
Moppet Options
Moppet XR
In response to customer feedback, Cook Compression translated the proven success of the Moppet valve in severe service environments to a new design that delivers extended run times in small-diameter applications. The engineered-to-order Moppet XR valve delivers the same reliability and durability as traditional MOPPET valves while maintaining high gas flow in tight clearance applications. MOPPET XR valve design characteristics help reduce energy costs, and withstand severe service conditions to deliver extended run times.
E2 Valve Elements
Elastomer-enhanced elements absorb energy to tolerate higher impacts than metallic and thermoplastic designs. They have a unique ability to flex and conform to valve seats to retain a gas-tight seal and protect the seat surface in very dirty applications, such as flare gas. This results in an extended valve service life and reduced maintenance costs.
Moppet XR for Maximized Flow
Building on the proven success of the MOPPET valve in severe service environments, Cook Compression has introduced the Moppet XR with new features to improve efficiency:
- A new smaller MOPPET disc offers more options for configuration and improves flow area in smaller valves
- A new patented disc design optimizes central disc flow
- A milled seat design allows optimization of flow area
- An optimized guard design further increases efficiency
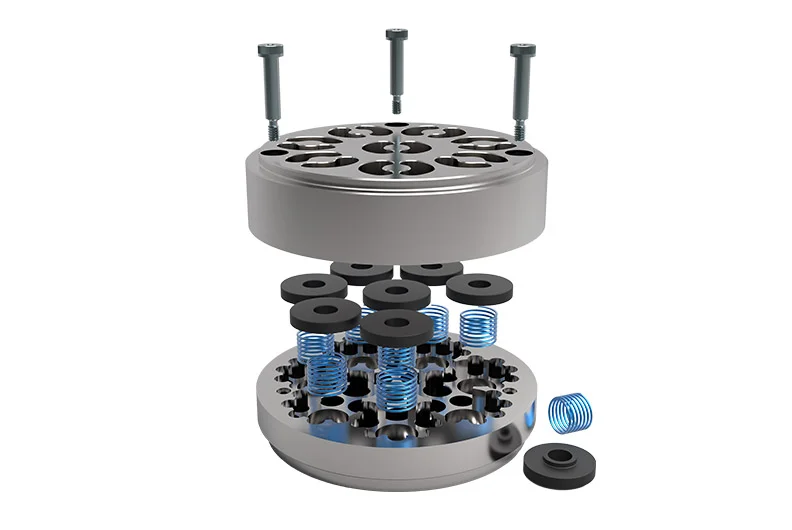
Advantages
- Superior reliability
- Rugged construction
- Expanded operating range and range of physical sizes
- Interchangeable discs for economical inventory
- Available with finger and plug unloaders
- Now with options for small-diameter spaces
- Optional elastomer elements for tighter seals and longer run times
Typical Applications
- Flare gas
- Dirty natural gas
- Hydrogen
- Polypropylene
- Other severe service environments
Related Case Studies
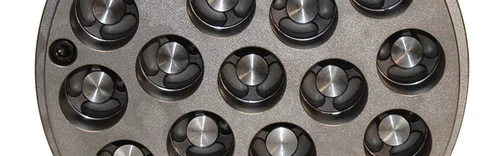
Offshore Producer More Than Doubles Valve Run Times
